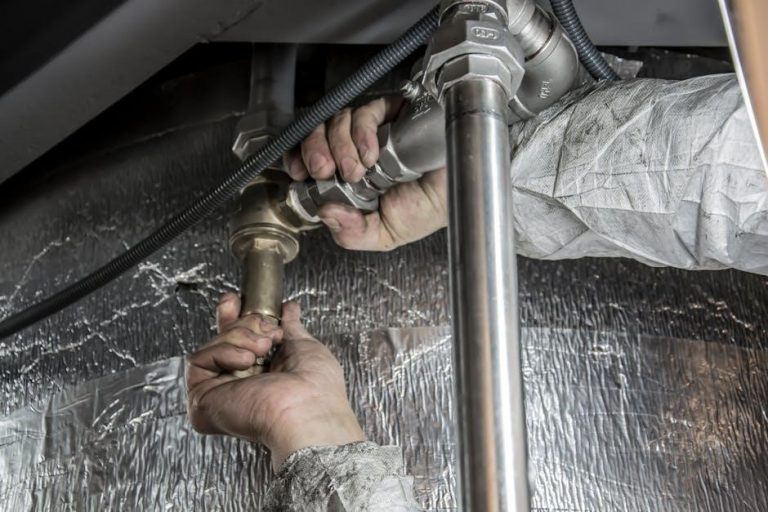
Valve guide seals are critical engine components located in the cylinder head, ensuring proper valve operation by preventing oil leakage․ They play a vital role in maintaining engine efficiency and performance, as well as preventing oil from entering the combustion chamber․
1․1 Definition and Purpose
Valve guide seals are components in an engine’s cylinder head that prevent oil from leaking into the combustion chamber․ Their primary purpose is to ensure proper valve operation by sealing the gap between the valve stem and the valve guide․ This prevents oil from entering the combustion chamber, reducing emissions and maintaining engine efficiency․ They are essential for preventing oil leakage and ensuring optimal engine performance․
1․2 Importance in Engine Performance
Valve guide seals are crucial for maintaining engine performance by preventing oil leakage into the combustion chamber․ This reduces emissions and ensures efficient combustion, leading to better fuel efficiency and lower oil consumption․ Worn seals can cause blue smoke from the exhaust, increased oil use, and reduced engine efficiency․ Properly functioning seals contribute to optimal engine power, lower emissions, and overall engine longevity․ Regular inspection and maintenance are essential to prevent these issues and maintain peak engine performance․
Function and Operation
Valve guide seals prevent oil leakage into combustion chambers by tightly sealing valve stems, ensuring proper engine operation and efficiency․
2․1 Role in Preventing Oil Leakage
Valve guide seals play a crucial role in preventing oil leakage by forming a tight barrier around the valve stem․ This prevents engine oil from seeping into the combustion chamber, which could lead to blue smoke from the exhaust and increased oil consumption․ Proper sealing ensures efficient engine performance and prevents contamination of the combustion process, maintaining optimal engine health and efficiency․
2․2 Mechanism of Sealing
Valve guide seals create a tight barrier around the valve stem, preventing oil from leaking into the combustion chamber․ This is achieved through a combination of precise design and materials that ensure a snug fit․ The seals work in conjunction with the valve guide to maintain proper engine performance․ When functioning correctly, they prevent oil contamination in the combustion process, ensuring efficient engine operation and minimizing the risk of oil-related issues․ Proper sealing is essential for maintaining engine health and efficiency over time․
Types of Valve Guide Seals
Valve guide seals are available in various designs, including O-Ring, Teflon, and Umbrella seals․ Each type is engineered to provide optimal sealing performance in different engine conditions․
3․1 O-Ring Seals
O-Ring seals are a popular choice for valve guide applications due to their reliability and durability․ These seals are typically made from rubber or synthetic materials, designed to withstand engine heat and wear․ They provide a tight fit around the valve stem, effectively preventing oil leakage into the combustion chamber․ O-Ring seals are known for their simplicity and ease of installation, making them a cost-effective solution for maintaining engine performance and efficiency․ Their consistent sealing capability ensures optimal engine operation․
Teflon seals are another type of valve guide seal, known for their non-stick properties and resistance to high temperatures․ They are often used in high-performance engines where reliability is crucial․ Teflon seals provide a tighter seal compared to traditional O-rings, reducing oil leakage effectively․ Their durability makes them a preferred choice for engines subjected to heavy use․ However, Teflon seals can be more expensive and complex to install, requiring precise fitment to ensure optimal performance․ Despite this, they offer superior longevity and performance in demanding engine conditions․ Umbrella seals are a type of valve guide seal designed to provide a secure fit around the valve stem, preventing oil leakage into the combustion chamber․ Their unique design features a spring-loaded mechanism that ensures a tight seal even under high engine temperatures․ Made from durable materials, umbrella seals are effective in reducing oil consumption and emissions․ They are commonly used in automotive and industrial engines, offering a reliable solution for maintaining engine efficiency and performance over time․ Worn valve guide seals often cause blue smoke from the exhaust, increased oil consumption, and reduced engine efficiency, signaling the need for prompt inspection and replacement․ Blue smoke from the exhaust is a common indicator of worn valve guide seals․ This occurs when engine oil leaks into the combustion chamber and is burned, producing a distinctive blue tint in the exhaust gases․ The smoke is typically more noticeable during acceleration or when the engine is under load․ If left unaddressed, this issue can lead to further engine damage, making prompt inspection and repair essential to maintain engine health and performance․ Worn valve guide seals can lead to increased oil consumption as engine oil leaks into the combustion chamber and is burned during the engine cycle․ This results in the need for frequent oil refills and higher maintenance costs․ Additionally, it can cause reduced fuel efficiency and increased emissions․ If left unchecked, the issue may progress, potentially damaging other engine components․ Regular inspections and timely replacements are essential to prevent these complications and maintain optimal engine performance․ Worn valve guide seals can significantly reduce engine efficiency by allowing oil to enter the combustion chamber, leading to decreased power output․ This results in poor fuel efficiency and increased emissions․ Over time, the accumulated oil residue can foul spark plugs and clog fuel injectors, further diminishing performance․ If left unaddressed, the issue may escalate, causing more severe damage to engine components and requiring costly repairs․ Regular maintenance and prompt seal replacement are crucial to uphold engine efficiency and overall vehicle performance․ Valve guide seal failure is primarily caused by wear and tear over time, high mileage, and poor maintenance practices, which degrade the seals’ integrity gradually․ Wear and tear over time is a primary cause of valve guide seal failure․ As engines operate, the seals experience constant friction and heat, leading to gradual degradation․ Prolonged exposure to these conditions weakens the material, causing the seals to lose their effectiveness․ This natural deterioration is inevitable but can be slowed with proper lubrication and regular maintenance․ Over time, the seals may develop cracks or become brittle, ultimately failing to prevent oil leakage and maintain engine performance․ High mileage significantly contributes to valve guide seal failure․ As vehicles accumulate miles, the seals endure extensive wear from repeated valve stem movements․ This prolonged use leads to material fatigue and eventual loss of sealing integrity․ Engines with high mileage often exhibit oil leakage due to compromised seals, which can result in blue smoke from the exhaust and increased oil consumption․ Regular inspections and timely replacements are crucial to prevent further engine damage and maintain performance․ Poor maintenance is a primary contributor to valve guide seal failure; Infrequent oil changes and lack of regular inspections allow contaminants to accumulate, accelerating seal degradation․ Neglecting to address worn components or improper installation of seals can lead to premature failure․ Additionally, inadequate lubrication and insufficient inspection of valve train components exacerbate wear․ Over time, this neglect results in oil leakage and reduced engine performance․ Proper maintenance schedules and attention to detail are essential to extend the lifespan of valve guide seals․ Replacing valve guide seals requires precise tools and techniques to ensure proper fitment and function, avoiding further engine damage and maintaining optimal performance․ Replacing valve guide seals demands specific tools and materials to ensure a proper fit and function․ Essential tools include a valve spring compressor, screwdrivers, pliers, a socket set, and a torque wrench․ Materials needed are new seals, lubrication, a gasket set, and cleaning supplies․ Ensure the valve train is securely held during the process to avoid damage․ Always use high-quality seals and follow manufacturer guidelines for optimal results and longevity of the engine․ Proper tools and materials are crucial for a successful replacement․ The installation begins with removing the cylinder head and disassembling the valve train components․ Compress the valve springs to access the old seals․ Carefully extract the worn seals and clean the area․ Apply a thin layer of lubricant to the new seals before sliding them into place․ Reassemble the valve train, ensuring proper alignment and tension․ Reinstall the cylinder head and gasket, then torque the bolts as specified․ Finally, test the engine to confirm the seals are functioning correctly and there are no leaks․ To ensure proper sealing, clean the valve guide area thoroughly before installation․ Apply a thin, even layer of engine oil or silicone-based lubricant to the new seals․ Use a valve spring compressor to avoid damaging components during installation․ Align the seals precisely with the guides to prevent misplacement․ Tighten all related components in the specified sequence and torque to manufacturer recommendations․ Avoid over-tightening, which can damage the seals or guides․ Finally, perform a leak test after installation to confirm the seals are functioning correctly․ Proper technique ensures longevity and optimal engine performance․ Valve guide seals are typically made from durable materials like Viton, Teflon, or stainless steel, ensuring resistance to heat and wear․ Modern manufacturing employs CNC machining and 3D printing for precise, high-quality seals․ Valve guide seals are typically made from durable materials such as Viton, Teflon, and stainless steel․ These materials are chosen for their excellent resistance to heat, wear, and chemical degradation․ Viton, a fluorocarbon elastomer, offers superior sealing properties and durability in high-temperature environments․ Teflon, known for its non-stick surface, reduces friction and enhances lubrication․ Stainless steel is often used in high-stress applications due to its strength and corrosion resistance․ The choice of material depends on the engine’s operating conditions and the desired performance characteristics․ Modern seals often combine these materials for optimal performance․ Modern valve guide seals are manufactured using advanced techniques such as CNC machining and 3D printing for precision and consistency․ Laser cutting is employed to achieve intricate geometries, while automated assembly lines ensure efficiency and quality control․ These methods allow for the production of seals with tight tolerances, ensuring optimal performance and durability․ High-tech materials like Viton and Teflon are processed under controlled conditions to meet stringent automotive standards, making the seals resistant to extreme temperatures and wear․ Valve guide seals are essential in automotive engines for preventing oil leakage and ensuring efficient combustion․ They are also used in motorcycle engines and industrial engines, where durability and precise sealing are critical to performance and longevity․ In automotive engines, valve guide seals are crucial for maintaining optimal performance and reducing oil consumption․ They prevent oil from leaking into combustion chambers, minimizing emissions and improving fuel efficiency․ Modern automotive engines often feature advanced materials and designs for these seals, ensuring longevity and reliability under varying driving conditions․ Regular inspection and maintenance of these seals are essential to prevent engine damage and ensure smooth operation over time․ In motorcycle engines, valve guide seals are essential for performance and reliability due to the high-revving nature of these powertrains․ They prevent oil leakage into combustion chambers, reducing smoke emissions and maintaining engine efficiency․ Motorcycles often experience harsher conditions, making durable seals crucial․ Regular maintenance is vital to prevent premature wear, ensuring optimal engine function and minimizing the need for costly repairs․ Proper sealing also contributes to consistent power delivery, which is critical for riders seeking responsive handling and performance․ In industrial engines, valve guide seals are crucial for maintaining performance under heavy-duty conditions․ These engines operate at high loads and require durable seals to prevent oil leakage and ensure efficient combustion․ The seals are designed to withstand extreme temperatures and pressures, minimizing downtime and extending engine lifespan․ Proper sealing in industrial applications is vital for consistent power output and reducing operational costs․ Their reliability ensures smooth operation in demanding environments, making them a key component in industrial machinery and systems․ DIY valve guide seal replacement can save costs but requires mechanical skills and tools․ Professional repair ensures precision and reliability, often preferred for critical engine work․ DIY replacement of valve guide seals offers cost savings and hands-on learning․ It requires mechanical aptitude and specialized tools, posing risks of improper installation․ Success demands precision to avoid further damage․ While it can be rewarding, errors may lead to engine issues, making professional help sometimes necessary for complex cases․ Proper guidance and experience are crucial for a successful outcome, ensuring reliability and performance; Consulting a professional is advisable when symptoms persist or worsen, such as excessive oil consumption or blue smoke․ Experts have the tools and experience to accurately diagnose and repair issues, ensuring proper sealing and preventing further engine damage․ They can also address related problems, like worn guides, which require precision machining․ For complex cases or high-mileage vehicles, professional intervention is crucial to maintain engine performance and longevity, avoiding costly future repairs․ Valve guide seal replacement costs average $100-$300, depending on seal quality and labor fees․ High-performance seals may incur additional expenses․ The cost of replacement valve guide seals varies depending on the type and quality of the seals․ Basic O-ring seals are typically the most affordable, ranging from $5 to $15 per set․ Teflon and umbrella seals, offering superior durability and performance, can cost between $20 to $50 per set․ High-end or specialized seals, designed for high-performance engines, may range from $50 to $100 or more, depending on the manufacturer and specific features․ Labor costs for valve guide seal replacement can vary significantly depending on the mechanic’s expertise, workshop rates, and engine complexity․ On average, labor costs range from $300 to $800, with some high-performance or complex engines potentially costing more․ DIY replacement can save on labor costs but requires specialized tools and mechanical knowledge․ Proper installation is crucial to ensure longevity and prevent future issues, making professional labor a worthwhile investment for many vehicle owners․ Regular inspection of valve guide seals helps identify wear early, preventing engine damage․ Proper lubrication and avoiding excessive mileage without maintenance are key to extending seal longevity․ Regular inspection of valve guide seals is essential to identify wear and potential leaks early․ Look for signs like blue smoke from the exhaust, increased oil consumption, and valve train noise․ These indicators suggest seal degradation․ Inspecting the valve guides during routine maintenance can prevent costly repairs․ Use a borescope to examine the seals for cracks or wear․ Addressing issues promptly ensures optimal engine performance and prevents further damage to the engine․ Regular checks are a proactive approach to maintaining engine health․ Proper lubrication is crucial for maintaining valve guide seals․ Use high-quality engine oil suitable for your vehicle to ensure smooth operation․ Regular oil changes prevent debris buildup that can damage seals․ Avoid over-lubrication, as it may attract dirt, leading to premature wear․ Ensure the valve train is well-lubricated during engine operation․ Always follow the manufacturer’s recommendations for lubricants to maintain optimal performance and longevity of the valve guide seals․ Regular lubrication maintenance helps prevent seal degradation and ensures efficient engine function․ Common issues with valve guide seals include oil leakage, blue smoke, and reduced engine efficiency․ Inspecting valve guides and seals can help identify the root cause․ Identifying oil leakage from valve guide seals involves inspecting the exhaust for blue smoke, checking cylinder head surfaces, and monitoring oil consumption levels․ Blue smoke typically indicates oil entering the combustion chamber, while excessive oil usage points to worn seals․ Visual inspection of valve guides and seals can reveal wear or damage․ Additionally, compression tests or leak-down tests can help pinpoint the source of the leak․ Diagnosing valve guide seal failure involves observing symptoms like blue smoke from the exhaust, increased oil consumption, and reduced engine efficiency․ A compression test can reveal low compression due to oil entering the combustion chamber․ Leak-down tests help identify air escaping through the valve guides․ Visual inspection of the valve train for excessive oil residue or wear on the seals confirms failure․ These steps ensure accurate diagnosis before proceeding with repairs or replacements․ A Toyota engine with excessive oil consumption and blue smoke was repaired by replacing worn valve guide seals, restoring performance and reducing emissions significantly․ A Toyota engine experiencing high oil consumption and blue smoke was successfully repaired by replacing worn valve guide seals․ This fix restored engine performance, eliminated smoke, and reduced emissions․ The repair involved inspecting the valve guides, replacing the seals, and ensuring proper installation; The outcome highlighted the importance of addressing seal wear promptly to maintain engine efficiency and prevent further damage․ This case underscores the effectiveness of seal replacement in resolving common engine issues․ A case involving premature valve guide seal failure revealed that improper installation and insufficient lubrication were primary causes․ Overlooking these factors led to rapid wear and oil leakage, causing engine inefficiency․ This failure emphasized the importance of following correct installation procedures and using high-quality materials․ Additionally, neglecting regular inspections contributed to the issue, highlighting the need for proactive maintenance to prevent such problems․ This experience serves as a valuable lesson in ensuring proper techniques and care in seal replacement processes․ Frequently Asked Questions about valve guide seals address common concerns, such as their lifespan, symptoms of failure, and repair options․ This section provides clear answers to help users understand and maintain their engine’s health effectively, ensuring optimal performance and preventing costly damages․ Valve guide seals typically last between 50,000 to 150,000 miles, depending on driving conditions and engine maintenance․ Proper lubrication and regular inspections can extend their lifespan․ However, aggressive driving or poor maintenance may reduce durability․ Replacing worn seals promptly is crucial to prevent oil leakage and maintain engine efficiency․ Always consult a professional for accurate assessments and timely replacements to avoid further engine damage and ensure optimal performance․ Driving with worn valve guide seals is possible but not advisable․ It can lead to increased oil consumption, reduced engine efficiency, and blue smoke from the exhaust․ Over time, this may cause further damage to engine components․ While short-term driving won’t cause immediate failure, prolonged use can exacerbate wear and potentially lead to more costly repairs․ It’s recommended to address the issue promptly to maintain engine health and performance․ Future trends in valve guide seals include innovative materials like self-healing coatings and advanced manufacturing techniques such as 3D printing, enhancing durability and sustainability․ Research focuses on advanced materials like graphene and nanomaterials for valve guide seals, offering enhanced durability and thermal resistance․ These innovations aim to reduce wear and improve engine efficiency, addressing issues like high-mileage degradation and extreme operating conditions․ Additionally, self-lubricating materials are being explored to minimize friction and extend seal lifespan, ensuring optimal performance in modern engines․ Modern manufacturing techniques, such as 3D printing and precision CNC machining, are revolutionizing valve guide seal production․ These methods enable tighter tolerances and complex geometries, enhancing seal performance․ Advanced surface coatings and automated assembly lines further improve consistency and durability․ Such innovations reduce production costs and lead times, ensuring higher-quality seals that meet the demands of contemporary engines․3․2 Teflon Seals
3․3 Umbrella Seals
Symptoms of Worn Valve Guide Seals
4․1 Blue Smoke from Exhaust
4․2 Increased Oil Consumption
4․3 Reduced Engine Efficiency
Causes of Valve Guide Seal Failure
5․1 Wear and Tear Over Time
5․2 High Mileage
5․3 Poor Maintenance
Replacement and Installation
6․1 Tools and Materials Required
6․2 Step-by-Step Installation Process
6․3 Tips for Proper Sealing
Materials and Manufacturing
7․1 Common Materials Used
7;2 Modern Manufacturing Techniques
Applications in Different Engines
8․1 Automotive Engines
8․2 Motorcycle Engines
8․3 Industrial Engines
DIY vs Professional Repair
9․1 Pros and Cons of DIY Replacement
9․2 When to Consult a Professional
Cost Factors
10․1 Cost of Replacement Seals
10․2 Labor Costs
Maintenance and Prevention
11․1 Regular Inspection
11․2 Lubrication Best Practices
Troubleshooting Common Issues
12․1 Identifying Oil Leakage Sources
12․2 Diagnosing Seal Failure
Case Studies and Real-World Examples
13․1 Success Stories of Seal Replacement
13․2 Lessons Learned from Failures
Frequently Asked Questions
14․1 How Long Do Valve Guide Seals Last?
14․2 Can I Drive with Worn Seals?
Future Trends and Innovations
15․1 Advanced Materials
15․2 Improved Manufacturing Processes